Korozja elektrochemiczna to proces niszczenia metali w środowisku elektrolitycznym, np. w wodzie. Zachodzi dzięki powstaniu ogniwa galwanicznego – różnicy potencjałów między metalami. Skutkuje degradacją materiałów, głównie poprzez utlenianie. Proces przyspiesza obecność tlenu, wilgoci i zanieczyszczeń. Powoduje straty w przemyśle.
Korozja elektrochemiczna stanowi jeden z najpoważniejszych problemów w przemyśle, powodując spore straty ekonomiczne i zagrożenia bezpieczeństwa. W warunkach atmosferycznych metal ulega stopniowej degradacji poprzez reakcje utleniania i redukcji zachodzące na jego powierzchni. Proces ten rozpoczyna się od utworzenia ogniwa galwanicznego, gdzie metal staje się anodą oddając elektrony, podczas gdy tlen z powietrza pełni rolę katody. Zjawisko korozji elektrochemicznej jest szczególnie intensywne w środowiskach o wysokiej wilgotności i zawartości zanieczyszczeń atmosferycznych. Różnice potencjałów elektrochemicznych między poszczególnymi obszarami powierzchni metalu prowadzą do powstania mikroogniw korozyjnych. Powstające produkty korozji mogą tworzyć warstwy pasywacyjne lub przyspieszać dalszą degradację materiału.
Mechanizm korozji elektrochemicznej opiera się na jednoczesnym występowaniu procesów anodowych i katodowych. Najczęstszymi formami zniszczeń korozyjnych są: korozja równomierna, wżerowa, międzykrystaliczna i naprężeniowa. W środowisku przemysłowym szczególnie niebezpieczna jest korozja galwaniczna, występująca na styku dwóch różnych metali. Intensywność procesu korozji zależy od wielu spraw: temperatury, pH środowiska, stężenia tlenu oraz obecności jonów chlorkowych i siarczanowych. Na szybkość procesu wpływają także naprężenia mechaniczne i mikrostruktura materiału.
Klasyfikacja i monitoring procesów korozyjnych
- Korozja atmosferyczna
- Korozja galwaniczna
- Korozja szczelinowa
- Korozja wżerowa
- Korozja międzykrystaliczna
- Korozja naprężeniowa
- Korozja zmęczeniowa
Monitoring procesów korozyjnych wymaga zastosowania specjalistycznych metod badawczych: Podstawowymi technikami są pomiary potencjału elektrochemicznego, badania impedancyjne oraz analiza mikroskopowa powierzchni. „Ważne znaczenie ma właściwa interpretacja wyników pomiarów oraz dobór odpowiednich metod ochrony przeciwkorozyjnej”. Zjawisko korozji elektrochemicznej może prowadzić do całkowitej degradacji konstrukcji metalowych (szczególnie w przypadku elementów infrastruktury krytycznej). Czy możliwe jest całkowite powstrzymanie procesów korozyjnych? W praktyce przemysłowej stosuje się różnorodne metody zabezpieczeń: od powłok ochronnych po ochronę katodową i anodową.
Innowacyjne metody zapobiegania korozji
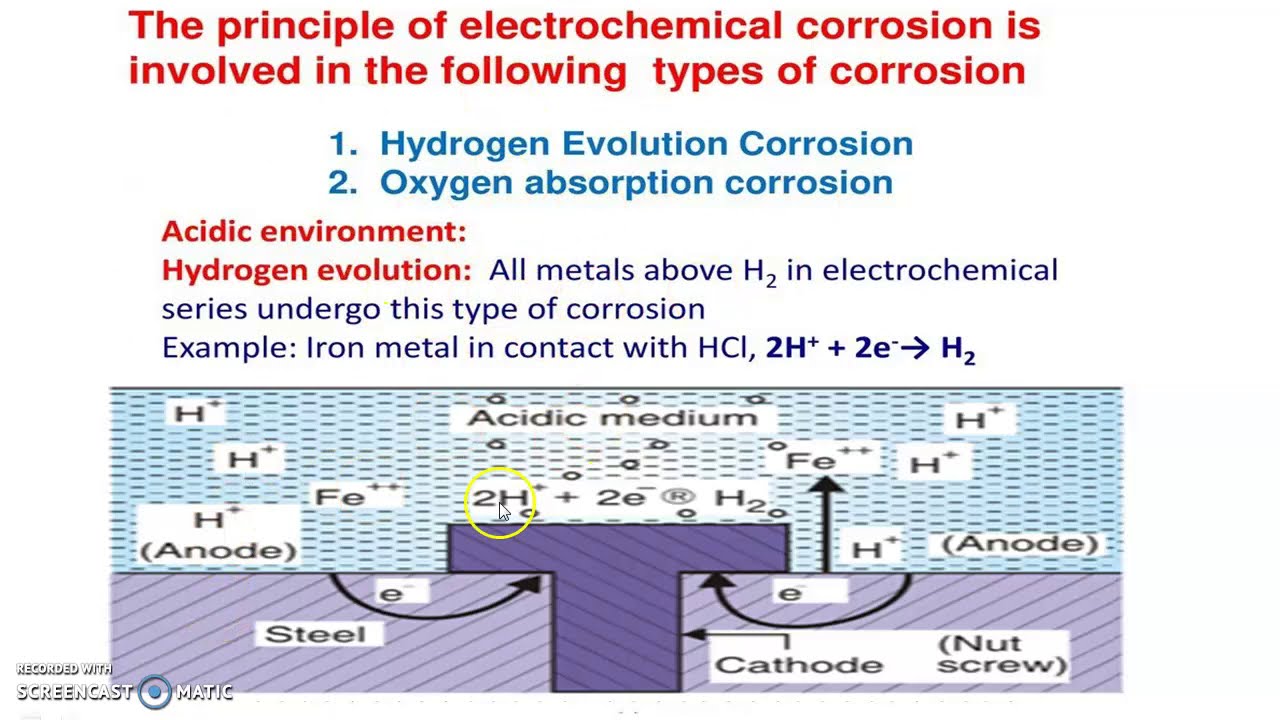
Rozwój nanotechnologii otworzył nowe możliwości w dziedzinie ochrony przeciwkorozyjnej. Wykorzystanie inteligentnych powłok mających nanocząstki pozwala na samoczynną naprawę uszkodzeń powierzchni. Czy nanocząstki mogą revolucjonizować ochronę przeciwkorozyjną? Badania nad nowymi materiałami – jak nanokompozytowy grafen – wskazują na ich wysoką skuteczność w hamowaniu procesów korozyjnych. Monitoring stanu konstrukcji odbywa się obecnie przy użyciu zaawansowanych czujników (wykorzystujących zjawiska elektrochemiczne i optyczne).
Ukryty zabójca metali: korozja elektrochemiczna – co trzeba o niej wiedzieć
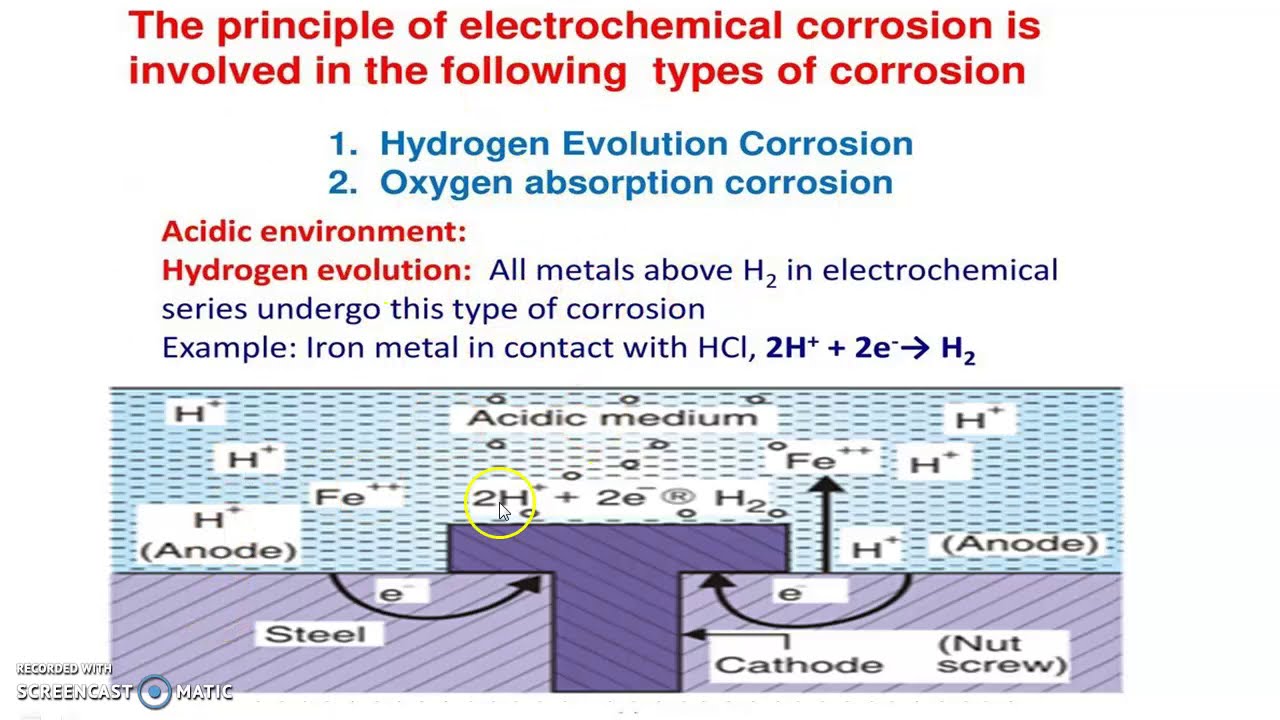
Korozja elektrochemiczna jest procesem niszczenia metali w wyniku reakcji utleniania i redukcji, zachodzących na powierzchni metalu w kontakcie z elektrolitem. Proces ten wymaga obecności anody, katody oraz przewodnika jonowego, tworząc ogniwo korozyjne. Utlenianie metalu zachodzi na anodzie, gdzie metal przechodzi do roztworu w postaci jonów, podczas gdy na katodzie następuje redukcja utleniacza.
Wyróżnia się parę podstawowych rodzajów korozji elektrochemicznej. Korozja równomierna rozwija się z jednakową szybkością na całej powierzchni metalu. Korozja wżerowa tworzy głębokie ubytki w materiale, szczególnie niebezpieczne w instalacjach ciśnieniowych. Korozja międzykrystaliczna postępuje wzdłuż granic ziaren, osłabiając strukturę metalu. Korozja szczelinowa występuje w wąskich szczelinach i połączeniach elementów. Korozja selektywna atakuje wybrane składniki stopów, a korozja naprężeniowa rozwija się pod wpływem jednoczesnego działania środowiska korozyjnego i naprężeń mechanicznych.
Wyjątkowe strategie ochrony przed żywiołem korozji w środowisku przemysłowym
Ochrona instalacji przemysłowych przed korozją stanowi fundamentalne wyzwanie dla utrzymania długoterminowej sprawności operacyjnej zakładów. Właściwe zabezpieczenie antykorozyjne może wydłużyć żywotność instalacji nawet o 300%. Nowoczesne metody obejmują także pasywnei aktywne systemy ochrony, wykorzystując zaawansowane powłoki organiczne oraz technologie elektrochemiczne.
- Powłoki galwaniczne
- Inhibitory korozji
- Ochrona katodowa
- Specjalistyczne farby przemysłowe
- Powłoki metaliczne natryskiwane cieplnie
Podstawowym aspektem jest regularna kontrola stanu zabezpieczeń oraz monitoring warunków środowiskowych, które mogą przyspieszać procesy korozyjne. Uwagę należy zwrócić na miejsca łączenia różnych materiałów, gdzie ryzyko korozji galwanicznej jest najwyższe.
Innowacyjne nanopowłoki w zabezpieczeniach antykorozyjnych
Przełomowym rozwiązaniem w dziedzinie ochrony antykorozyjnej są nanopowłoki z dodatkiem grafenu. Ta technologia umożliwia tworzenie ultracie nkich warstw ochronnych o niespotykanej dotąd odporności na agresywne środowiska przemysłowe. Zastosowanie nanocząstek w powłokach pozwala na uzyskanie efektu samonaprawiania się mikrouszkodzeń, co mocno zwiększa skuteczność ochrony.
Elektrochemiczna tarcza dla podziemnej infrastruktury
Metalowe konstrukcje zakopane w ziemi są narażone na korozję elektrochemiczną wywołaną przez agresywne środowisko gruntowe oraz prądy błądzące. Ochrona katodowa stanowi skuteczną metodę zabezpieczenia rurociągów i zbiorników podziemnych przed degradacją korozyjną. Polega na wytworzeniu różnicy potencjałów między chronioną konstrukcją a otaczającym gruntem, za pomocą czego metal staje się katodą i nie ulega utlenianiu.
W praktyce stosuje się dwie metody ochrony katodowej: galwaniczną (protektorową) wykorzystującą anody magnezowe lub cynkowe oraz z zewnętrznym źródłem prądu. Każda z nich wymaga częstego monitorowania parametrów elektrycznych i okresowych pomiarów kontrolnych.
Prawidłowo zaprojektowana i eksploatowana instalacja ochrony katodowej może wydłużyć żywotność chronionej konstrukcji nawet o parędziesiąt lat, mocno redukując koszty związane z remontami i wymianą infrastruktury. Skuteczność ochrony zależy od właściwego doboru parametrów technicznych oraz częstej konserwacji systemu.